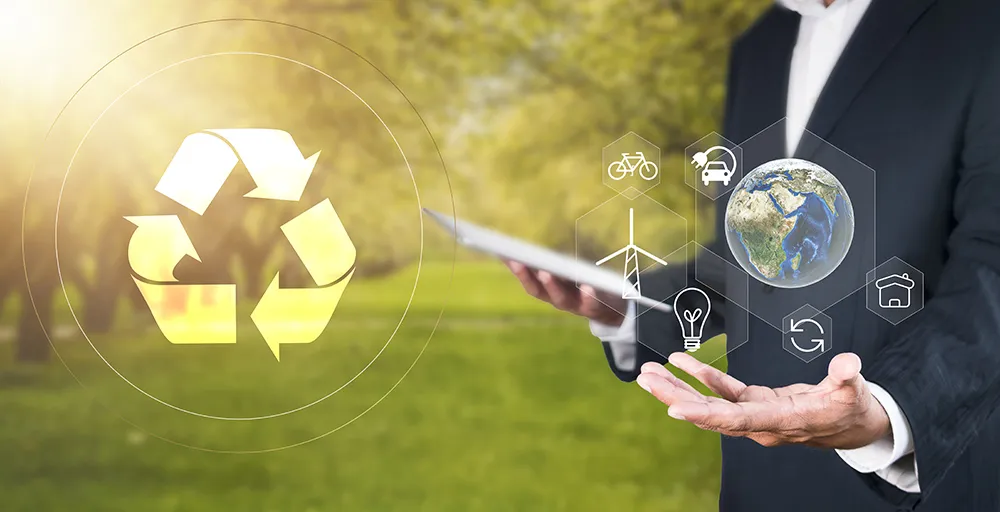
Circular Economy
Technological Innovations Propel Plastic Recycling Forward
Since the advent of plastics, their remarkable performance and widespread applications have fundamentally transformed industrial production and lifestyle; however, they have also posed challenges for environmental protection. From the perspective of a circular economy for plastics, achieving the recycling, processing, and reuse of post-consumer plastics has become an area of collaboration and exploration for many global well-known brands, product manufacturers, and recycling line manufacturers.
According to a report by Grand View Research, the global market size for recycled plastics is expected to be US$55.98 billion in 2024. The annual compound growth rate from 2024 to 2030 is projected to reach 9.5%, increasing to US$96.48 billion.
In recent years, substantial progress has been made in mechanical and chemical recycling, technological breakthroughs in high-value recycled plastics, and the expansion of applications across various sectors.
Source: Adsale Plastics Network(www.AdsaleCPRJ.com)
Mechanical recycling remains the primary method for plastic recycling, with advancements towards multidimensional innovation and large-scale expansion. Key trends include digitalization and modularization, improvement of sorting and purification efficiency, and optimization of process flows.
AI Visual Sorting Systems
In the pre-processing stage, artificial intelligence (AI) visual sorting systems can effectively enhance sorting efficiency. For example, Krones' intelligent sorting line uses multispectral imaging technology, capable of identifying batches of PET bottle flakes with color differences of less than 5%, achieving a sorting accuracy rate of 99.2% and sorting efficiency that is 3 times higher than traditional manual methods.
The AI-powered plastic whole bottle sorting machine from Hefei Taihe Intelligent Technology employs a deep learning algorithm to autonomously collect material characteristic information. Featuring precise multispectral recognition, it achieves a purification rate of over 98%.
Modular Crushers and Washing Lines
Plastic recycling equipment is rapidly progressing towards modularization and integration. The new generation of crushers and washing lines employs function modules that can be flexibly integrated, facilitating easy maintenance and upgrades. Their compact layout saves space, while the advantages of an integrated system allow for the consolidation of various stages of the recycling process into an intelligent assembly line, further reducing energy consumption and wastewater discharge.
ENMA's latest modular crusher is designed to reduce the need for different types of crushers by minimizing waste and optimizing the space of recycling facilities, thereby enhancing recycling efficiency. This is primarily due to the easy disassembly and reassembly of its modular components, which reduces production complexity and enables standardized mass production, thus shortening delivery times for customers.
Regarding washing lines, Zhejiang BoReTech Environmental Engineering has introduced a new generation of PET bottle washing lines — ES process — which features integrated equipment configurations and excellent washing performance to support the recycling of high-quality PET flakes. This washing line employs a highly modular design, reducing its footprint by 25% while optimizing unit energy consumption, with a 25% improvement in downstream filtration performance.
Bottle-to-Bottle High-Value Closed-Loop Recycling Technology
Significant advancements have also been made in high-value closed-loop recycling applications. The PET bottle-to-bottle process represents a scalable application in the global plastic recycling sector with high-value recovery.
Starlinger's recoSTAR PET art PET bottle-to-bottle recycling system produces rPET materials that not only have high purity but also extremely low levels of acetaldehyde, ethylene glycol, and volatile organic compounds, while maintaining low energy consumption and a small footprint.
EREMA's VACUREMA technology has shown exceptional performance in the bottle-to-bottle recycling sector, where recycling and compounding are completed in a single processing step, making the entire process energy-efficient. Currently, there are over 400 EREMA PET systems compliant with food-grade standards in operation worldwide, with a total production capacity exceeding 4.5 million tons annually.
Chinese companies are also continuously gaining international recognition for their bottle-to-bottle recycling and pelletizing technologies. Last year, ACERETECH's safPET bottle-to-bottle pelletizing process and equipment for removing contaminants and enhancing adhesion successfully received a No Objection Letter (NOL) from the FDA.
In recent years, global capacity for chemical recycling of plastics has steadily increased. In Europe, tens of thousands tons of capacity have been already operational, with over 5 million tons under construction, of which about 1 million tons are in China. Leading chemical companies such as BASF, ExxonMobil, and SK Chemicals are launching new projects and facilities worldwide.
BASF continues to advance its ChemCycling project, chemically recycling benzene from plastic waste for use in producing its Ccycled product line. The company utilizes pyrolysis technology to convert mixed plastic waste that has not yet been mechanically recycled into pyrolysis oil, serving as an alternative to fossil raw materials in its production networks across Europe, North America, and the Asia-Pacific region. Pyrolysis technology is also employed in ExxonMobil's Exxtend chemical recycling process, which transforms waste plastics into new plastic raw materials.
SK Chemicals' ECOTRIA CR circular copolyesters address the issue of plastic waste by utilizing its advanced chemical recycling method, Circular Recycle, which increases the utilization rate of recyclable plastic waste threefold. Traditional mechanical recycling can only process high-quality plastic waste (such as clear bottles), while Circular Recycle can purify and reuse a wider range of lower-quality plastic waste, including colored bottles, films, and textiles.
As both mechanical and chemical recycling technologies continue to advance, costs are gradually decreasing, leading to an expansion of market applications. Beyond traditional sectors like packaging and building materials, these plastic recycling technologies are finding broader applications in high-end industries such as automotive, electronics, textiles, and healthcare, meeting the demand for high-quality and sustainable materials across various sectors.
Driven by policies, market demand, and technological innovation, collaborations in car-to-car plastic recycling have accelerated in recent years. The EU's End-of-Life Vehicle (ELV) directive requires automobile manufacturers to use a certain percentage of recycled plastics in new vehicles, with a target of at least 25% recycled plastic by 2030. This has prompted automotive companies to expedite their efforts in circular economy.
For example, Covestro is strengthening its collaboration with Ausell, Chinese plastics recycling specialist, through a new initiative aimed at establishing a closed-loop system for automotive plastics recycling in China. The two parties will recover plastics from discarded vehicle headlights for new interior and exterior applications, meeting the growing industry demand and regulatory requirements.
Wanhua Chemical has also launched modified rPC, rPP, and rPA12 materials with varying PCR content. These materials can be used in components such as automotive headlamp housings, dashboards, bumpers, and piping systems, achieving a closed-loop material cycle from car to car.
Textiles are one of the primary applications for recycled plastics, with recycled PET being the most prevalent in textile applications. The global market for recycled fibers continued its steady growth in 2024. As renowned international brands like Adidas and Nike develop plans to replace virgin polyester with recycled polyester, the recycled fiber market is set to expand further.
PUMA has implemented its textile recycling technology RE:FIBRE, replacing recycled polyester fibers in the production of all replica jerseys for football clubs and federations since last year. This technology can utilize any polyester materials to create new clothing, such as factory offcuts, faulty goods, or polyester from old garments, and it can recover the necessary materials from textiles of any colour.
Recycled polyester fiber, one of Zhejiang Jiaren New Materials' flagship products, boasts advantages such as high quality, multi-functionality, traceability, and sustainability. This sustainable recycled polyester product has found widespread application in various sectors, including sports, outdoor activities, fashion, home textiles, automotive, consumer electronics, food and beverage, cosmetics, home appliances, and healthcare.
As global attention to the plastic circular economy continues to grow, along with advancements in material and processing technologies, recyc