Thailand Retains a Leading Role as Industrial Powerhouse in Southeast Asia
Publish date: 2025-03-21
Thailand's industrial production has taken a big leap forward over the years as the country moves to become
Southeast
Asia's leading manufacturing hub. At the center of this industrial growth is the plastics industry, which has
evolved to
meet the demands of the manufacturing sector. Rising use of plastics in Thailand's key industries has put the
country's
plastic production on an upswing, and the challenges on how to properly utilize and dispose plastics are being
addressed
through innovative materials and processes.
Sustained industrial activities have fueled the demand for plastic products in applications such as packaging, building and construction, automotive, and pharmaceutical. However, alongside demand expansion, the government is implementing more stringent regulations on plastic use and disposal that push plastics manufacturers to adopt sustainable practices. The country is also seeing rising investments in biodegradable plastics and high-tech recycling technologies in response to the growing acceptance of recycled plastics in various application sectors.
Sustained industrial activities have fueled the demand for plastic products in applications such as packaging, building and construction, automotive, and pharmaceutical. However, alongside demand expansion, the government is implementing more stringent regulations on plastic use and disposal that push plastics manufacturers to adopt sustainable practices. The country is also seeing rising investments in biodegradable plastics and high-tech recycling technologies in response to the growing acceptance of recycled plastics in various application sectors.
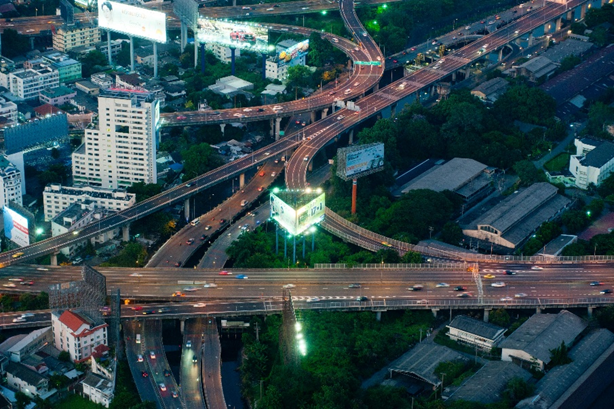
Sustained industrial activities in Thailand have created demand
for plastics.
(Source: Alex P/Pexels)
(Source: Alex P/Pexels)
Environmental Friendly Manufacturing Operations on the Rise
Major global companies are increasingly viewing Thailand as an ideal location for their manufacturing operations in
Southeast Asia. As the country works towards becoming the center for sustainable production, more and more
Thailand-based companies are setting up sustainable manufacturing operations in various locations across the
country.
This is largely driven by the growing awareness on the importance of proper plastic waste disposal and recycling to
alleviate climate change. In particular, the recycling of polyethylene terephthalate (PET) has intensified as this
material is considered as ideal for automotive as well as electronics and electric applications. PET resins are also
widely used in packaging due to the material's inherent strength, recyclability, and barrier properties.
Large-scale recycling operations are underway in Thailand. Indorama Ventures, the world's leading producer of PET, has tripled its plastics recycling operations to meet the increasing demand from beverage manufacturing companies in the region. The company has been acquiring PET recyclers in recent years as part of its strategy to boost the total recycling capacity from 250,000 tons to 750,000 tons annually by 2025. Another key player, ENVICCO Limited, a joint venture established by PTT Global Chemical focuses on sourcing, sorting, cleaning and recycling of plastic waste into reusable beads at an industrial estate in Rayong province. The recycled plastic beads from the project have a carbon footprint that is 60% lower than the original waste. The company aims to recycle more than 430,000 tons of plastic waste between 2023 and 2029, with an expected reduction of greenhouse gas emissions by 574,700 tons of carbon-dioxide equivalent.
Large-scale recycling operations are underway in Thailand. Indorama Ventures, the world's leading producer of PET, has tripled its plastics recycling operations to meet the increasing demand from beverage manufacturing companies in the region. The company has been acquiring PET recyclers in recent years as part of its strategy to boost the total recycling capacity from 250,000 tons to 750,000 tons annually by 2025. Another key player, ENVICCO Limited, a joint venture established by PTT Global Chemical focuses on sourcing, sorting, cleaning and recycling of plastic waste into reusable beads at an industrial estate in Rayong province. The recycled plastic beads from the project have a carbon footprint that is 60% lower than the original waste. The company aims to recycle more than 430,000 tons of plastic waste between 2023 and 2029, with an expected reduction of greenhouse gas emissions by 574,700 tons of carbon-dioxide equivalent.
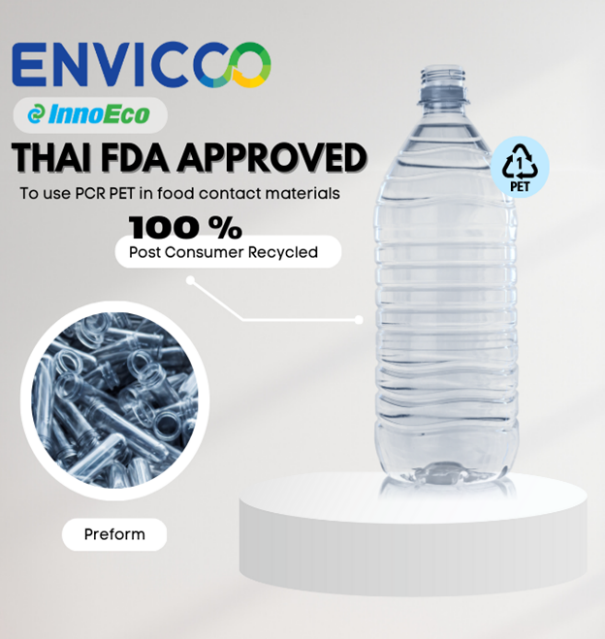
The recycled plastic beads from ENVICCO have a carbon footprint
that is 60% lower than the original waste.
(Source: ENVICCO)
(Source: ENVICCO)
Another project is the collaboration between Siam Cement Group (SCG) and Dow, aimed at recycling plastic waste in
the
Asia-Pacific region at a target annual capacity of 200,000 tons by 2030. SCG's chemical subsidiary and Dow signed a
memorandum of understanding (MOU) for the recycling facility. Additionally, SCG has partnered with Braskem to
establish
a THB 19.3 billion (€491.26 million) bio-ethylene plant with a capacity of 200,000 tons annually. This project has
received approval from the Thailand Board of Investment, and will be located at the Map Ta Phut Industrial Estate in
Rayong province. Braskem Siam plans to produce sugarcane-based bio-ethylene through bio-ethanol dehydration for the
production of “I'm green” bio-based polyethylene (PE). Braskem will contribute its EtE EverGreen technology while
SCG
Chemicals will provide expertise in high-quality PE grades for different applications targeting the Southeast Asian
market.
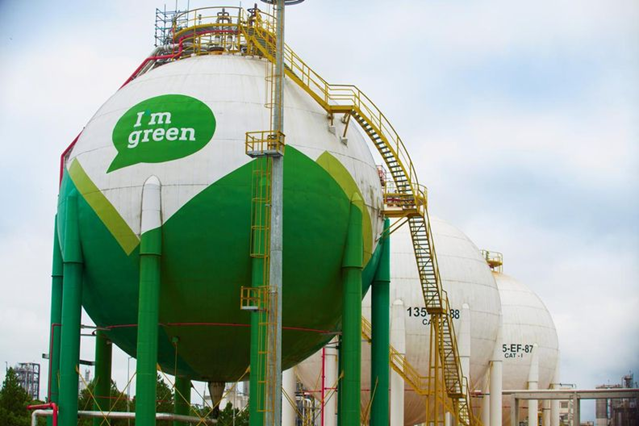
SCG has partnered with Braskem for a bio-ethylene plant with a
capacity of 200,000 tons annually.
(Source: Braskem)
(Source: Braskem)
EcoBlue, a plastics recycling company based in Rayong Province, has enhanced its recycling capabilities with the
installation of another Starlinger Viscotec SSP sorting and reprocessing plant. This commissioning marks a
significant
milestone in EcoBlue's journey toward becoming the largest recycler of high-quality food-grade resins in Thailand in
2024. The plant enables EcoBlue to offer a wide range of food-grade recycled resins, such as rPET, rHDPE and rPP,
all of
which conform to the standards set by the United States Food and Drug Administration (FDA).
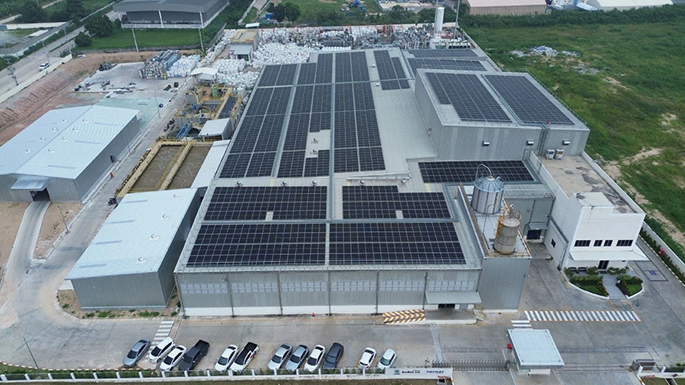
EcoBlue offers food-grade recycled resins produced at its plant
in
Rayong Province.
(Source: EcoBlue)
(Source: EcoBlue)
Green Innovations Expanding the Application of Recycled
Plastics
A growing number of Thai companies are driving innovations aimed at promoting sustainable practices. One notable
example
is Charoen Pokphand Foods Public Company Limited (CP Foods), which has ramped up its environmental conservation
efforts
by reducing single-use plastics and advocating for recyclable packaging across its supply chain. The company has
redesigned its packaging to enhance recyclability, and through collaboration with SCG Packaging Plc (SCGP) and SCG
Chemicals Plc (SCGC), CP Foods has adopted innovative pulp and polymer-based packaging and green plastic solutions
to
reduce greenhouse gas emissions. The company has been at the forefront of producing bioplastic food trays made from
polylactic acid (PLA) and has embraced 100% recyclable mono-plastic films.
Coca-Cola, another leader in sustainability, has introduced 1-liter bottles made from 100% recycled PET plastic. The company continues its “Coke Recycle Me with Trash Lucky” campaign, with giveaways to encourage Thai consumers to separate recyclable packaging from non-recyclable waste. Coca-Cola targets to make all of its packaging in the world to be recyclable by 2025, and to incorporate at least 50% recycled plastic in its packaging by 2030. It now offers at least one brand made from 100% recycled PET bottles (excluding caps and labels), in more than 40 countries around the world.
Coca-Cola, another leader in sustainability, has introduced 1-liter bottles made from 100% recycled PET plastic. The company continues its “Coke Recycle Me with Trash Lucky” campaign, with giveaways to encourage Thai consumers to separate recyclable packaging from non-recyclable waste. Coca-Cola targets to make all of its packaging in the world to be recyclable by 2025, and to incorporate at least 50% recycled plastic in its packaging by 2030. It now offers at least one brand made from 100% recycled PET bottles (excluding caps and labels), in more than 40 countries around the world.
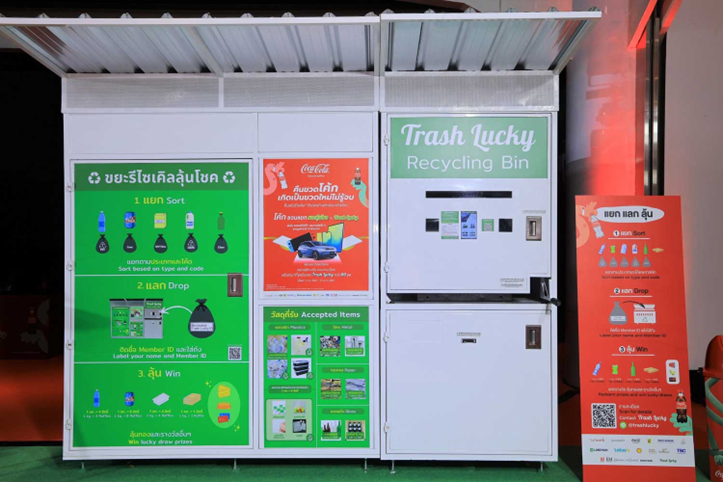
“Coke Recycle Me with Trash Lucky” campaign has been launched
by Coca-Cola to promote recycling.
(Source: Coca-Cola)
(Source: Coca-Cola)
In line with its goal to expand sustainable solutions, Makita Manufacturing (Thailand) Co., Ltd. and Dow announced
the
adoption of plastic cling film made with post-consumer recycled (PCR) resin in product logistics for the ease of
transportation. This initiative, in collaboration with MMP, a Thai packaging film manufacturer, incorporates up to
30%
PCR resin while maintaining performance and clarity comparable to traditional cling film from virgin plastics. With
flexibility and strength, the recyclable film is ideal for wrapping industrial crates for transportation, whether
manually or with machinery. This effort aims to reduce plastic waste by over 5 tons per year.
Similarly, Kao, a leading Japanese manufacturer of consumer products, has partnered with SCG Chemicals and Dow Thailand Group to develop packaging designed for recyclability. Kao plans to use this sustainable packaging across its product lines in Thailand. The collaboration marks an important step for Kao as it works towards its sustainability goals, including achieving carbon neutrality by 2050.
Similarly, Kao, a leading Japanese manufacturer of consumer products, has partnered with SCG Chemicals and Dow Thailand Group to develop packaging designed for recyclability. Kao plans to use this sustainable packaging across its product lines in Thailand. The collaboration marks an important step for Kao as it works towards its sustainability goals, including achieving carbon neutrality by 2050.
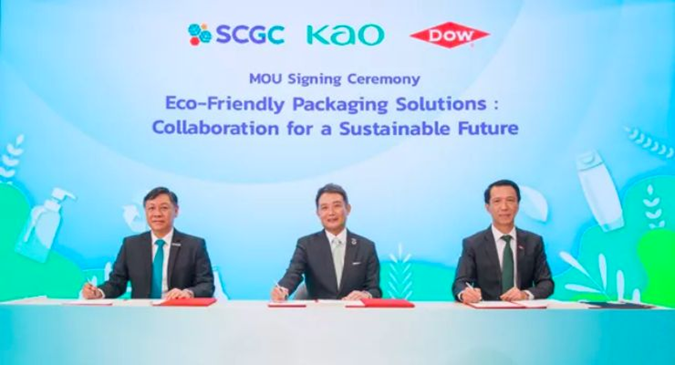
Kao has partnered with SCG Chemicals and Dow to develop
packaging designed for recyclability across its consumer
products portfolio.
(Source: Kao)
(Source: Kao)
Thailand's packaging sector is enhancing its innovation efforts on an
international scale. One example is Thai Union,
which has opened an innovation center in Wageningen, the Netherlands, as part of its R&D investments. The innovation
hub
focuses on product and packaging development for the company's seafood brands, and employs around 40 specialists,
including product, process, and packaging developers, as well as nutritionists, sensory and consumer scientists.
These
professionals collaborate with Thai Union's Global Innovation Center (GIC) in Bangkok. The innovation hub houses a
pilot
plant with capabilities of a full-scale Thai Union factory. It includes an analytical lab for physical and chemical
testing, a packaging lab for testing and prototyping new materials and functionality, a sensory lab to determine how
consumers will perceive any new products or packaging innovation, and a user experience kitchen to evaluate how
customers experience products.
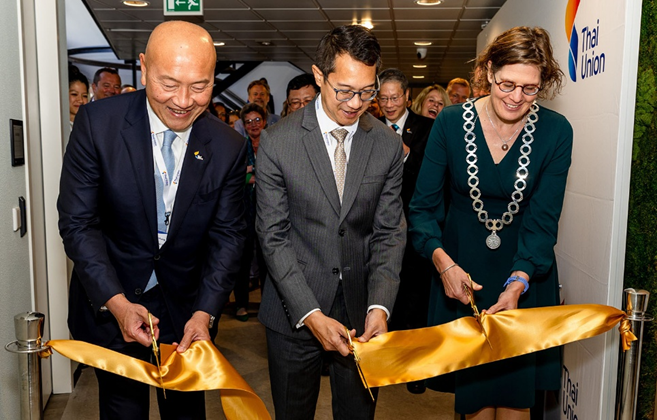
Thai Union has opened an innovation hub in Netherlands as part
of its
packaging development efforts.
(Source: Thai Union)
(Source: Thai Union)
As Thailand promotes sustainability through recycling in its industries, highly
advanced recycling technologies and
environmental friendly material solutions are essential.
At CHINAPLAS 2025, the plastics industry shift towards a circular economy will be showcased through innovative recycling technologies and plastic materials, offering manufacturers from Thailand and Southeast Asia more sustainable options. For more information, visit: www.chinaplasonline.com. www.chinaplasonline.com。
At CHINAPLAS 2025, the plastics industry shift towards a circular economy will be showcased through innovative recycling technologies and plastic materials, offering manufacturers from Thailand and Southeast Asia more sustainable options. For more information, visit: www.chinaplasonline.com. www.chinaplasonline.com。
About CHINAPLAS 2025
CHINAPLAS 2025, one of the world’s most prestigious international plastics and rubber trade fairs, will be held at Shenzhen World Exhibition & Convention Center (Bao’an), PR China from April 15-18, 2025. The exhibition will bring together over 4,000 international exhibitors under one roof and welcome visitors from across the globe, providing unmatched opportunities to explore the latest innovations and forge valuable connections.
The online pre-registration of CHINAPLAS 2025 has started. Pre-register NOW for an admission ticket at RMB 50 or USD 7.5. Pre-registered visitors shall receive their Visitor eBadges (for local visitors) or eConfirmation Letters (for overseas visitors). Admission tickets are available on a first-come, first-served basis.
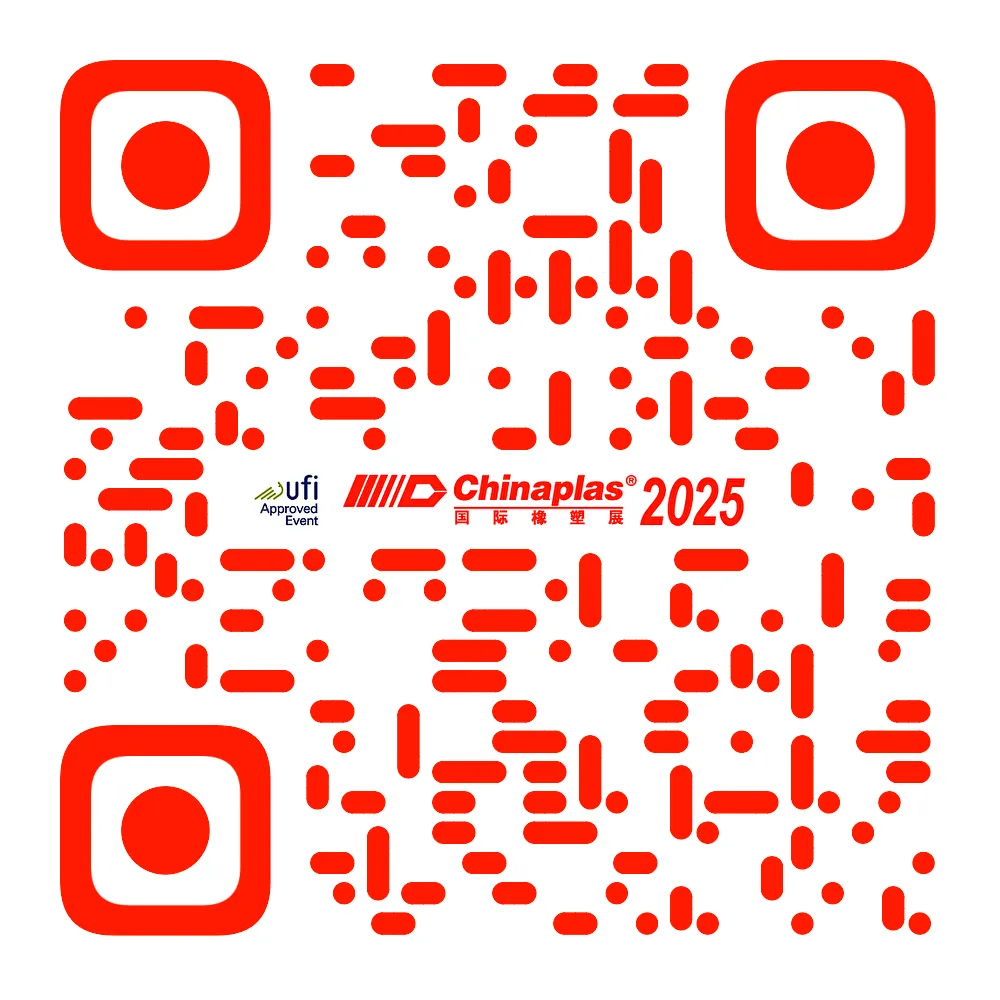
Besides the show days, the exhibition also enables buyers to connect with thousands of materials and machines suppliers all year round via CPS+ eMarketplace, a smart efficient integrated, and sustainable online sourcing platform which is complementary to the physical show of CHINAPLAS.
For more information, please visit: www.ChinaplasOnline.com.
CHINAPLAS 2025, one of the world’s most prestigious international plastics and rubber trade fairs, will be held at Shenzhen World Exhibition & Convention Center (Bao’an), PR China from April 15-18, 2025. The exhibition will bring together over 4,000 international exhibitors under one roof and welcome visitors from across the globe, providing unmatched opportunities to explore the latest innovations and forge valuable connections.
The online pre-registration of CHINAPLAS 2025 has started. Pre-register NOW for an admission ticket at RMB 50 or USD 7.5. Pre-registered visitors shall receive their Visitor eBadges (for local visitors) or eConfirmation Letters (for overseas visitors). Admission tickets are available on a first-come, first-served basis.
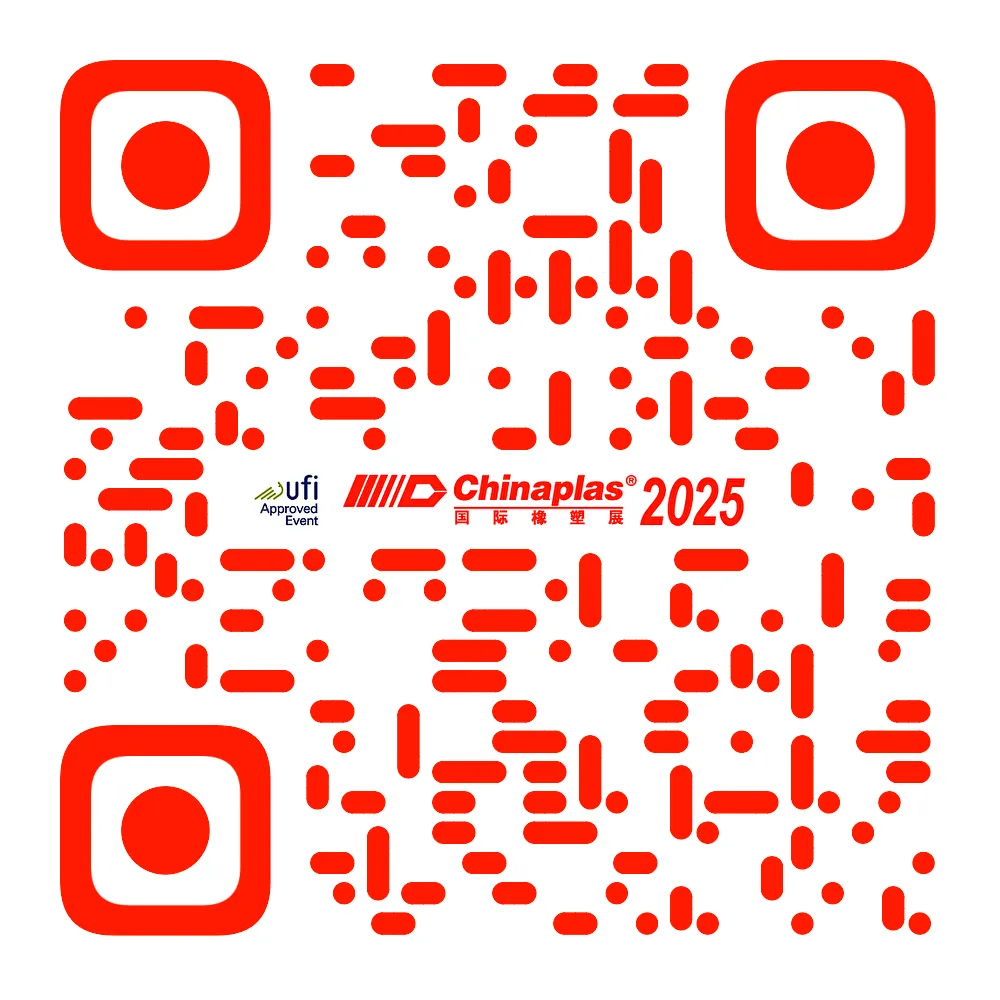
Scan to pre-register
Besides the show days, the exhibition also enables buyers to connect with thousands of materials and machines suppliers all year round via CPS+ eMarketplace, a smart efficient integrated, and sustainable online sourcing platform which is complementary to the physical show of CHINAPLAS.
For more information, please visit: www.ChinaplasOnline.com.